Our Top Products
5mm thick walls with thermal shock-resistant composition Mill Ceramic Jar
-
Grinding Ball Weight:1kg
Grinding Modes:Dry/Wet
Rotation Speed Ratio:2/3
Feeding Granularity:<=1mm
Maximum Loading Capacity:2/3 Capacity Of The Grinding Jar
Grinding Jar Volume:500ml
Thickness:5mm
Uses:Temperature-sensitive Protein Milling
Design:Integrated Vacuum Ports
Anti Wear Milling Tungsten Carbide Grinding Media 1mm-20mm OEM
-
For maximum lifespan: Use in WC-lined mills to prevent contamination.
For wet grinding: Compatible with water, alcohol, and most solvents.
Alternative for cost-sensitive applications: Zirconia (Y-TZP) or Si₃N₄ if hardness is sufficient.
MSDS Tungsten Carbide Grinding Media Sphere Beads 10mm In Bulk
-
✔ Excellent Chemical & Corrosion Resistance
Inert to most acids, alkalis, and solvents (except strong oxidizing acids like HNO₃).
No rust or oxidation – Unlike steel, suitable for wet grinding in corrosive environments.
✔ High Fracture Toughness (Better Than Alumina & Si₃N₄)
Toughness (KIC): 8–12 MPa·m¹/² (better than alumina and silicon nitride).
Resists chipping/cracking under high-impact milling conditions.
✔ Temperature Stability
Withstands high temperatures (up to 500–600°C without degradation).
Precision Cemented Tungsten Carbide Grinding Media Balls WC-Co Cobalt Bonded
-
Extreme Hardness & Wear Resistance
Hardness (HV): 1,800–2,200 (among the hardest grinding media available).
Superior abrasion resistance – 10–20x longer lifespan than steel balls in abrasive environments.
Minimal material loss – Ideal for high-precision grinding (e.g., ceramics, hard metals).
✔ High Density for Efficient Grinding
Density: 14.0–15.0 g/cm³ (much heavier than steel, ceramic, or Si₃N₄).
Higher kinetic energy – Improves grinding efficiency for hard, brittle materials.
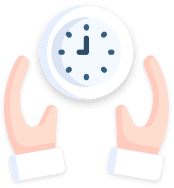
5mm thick walls with thermal shock-resistant composition Mill Ceramic Jar
-
Grinding Ball Weight:1kg
Grinding Modes:Dry/Wet
Rotation Speed Ratio:2/3
Feeding Granularity:<=1mm
Maximum Loading Capacity:2/3 Capacity Of The Grinding Jar
Grinding Jar Volume:500ml
Thickness:5mm
Uses:Temperature-sensitive Protein Milling
Design:Integrated Vacuum Ports
99.95% purity Ultra High Purity 3Y-TZP Jar for Nanotechnology
-
Grinding Ball Diameter:3mm, 5mm, 8mm, 10mm, 15mm
Grinding Ball Size:10 mm
Material:3 Mol% Yttria-stabilized Zirconia
Grinding Modes:Dry/Wet
Rotation Speed Ratio:2/3
Grinding Balls Material:Zirconia
Customization Options:Beneficial For Specialized Applications
Maximum Output Size:0.1μm
Warranty:1 Year
Hardness (HV):1,200–1,400
Extreme Environment Advanced Ceramic Grinding Jar 1500°C Capable
-
Application:Grinding And Mixing
Safety Features:Overload Protection
Grinding Ball Size:10mm
Vickers Hardness:1200–1400 HV
Feature:High Hardness And Strength
Material:3 Mol% Yttria-stabilized Zirconia
Extreme Environment:1500°C Capable
Eco-Friendly 95% Material Recovery Rate Recyclable Zirconia Ceramic Grinding Jar
-
Compatibility:Milling Equipment In Use
Capacity:2L
Purity:>99.9% ZrO₂
Density:6.05 G/cm³
Warranty:1 Year
Rotation Speed Ratio:2/3
Grinding Ball Size:10 mm
Grinding Ball Diameter:10 Mm
Fracture Toughness:6–10 MPa√m
Max Feeding Capacity:2/3 Capacity Of The Grinding Jar
Feature:High Hardness And Strength
Materials:3 Mol% Yttria-stabilized Zirconia
Solder Copper Phosphorus Metal Braze Paste 10g 500-800°C OEM
-
✔ Composition & Melting Behavior
Alloy Types:
CuP6 (Cu-6%P): Melting range 710–890°C (higher flow temp).
CuP8 (Cu-8%P): Melting range 710–800°C (most common).
CuP8+Ag (Cu-7.5%P-0.2%Ag): Improved ductility & strength.
Self-Fluxing: Phosphorus (P) removes oxides, eliminating need for separate flux (for copper-to-copper joints).
✔ Mechanical & Joint Properties
Shear Strength: 150–220 MPa (depends on base metal and joint clearance).
Electrical Conductivity: ~15–20% IACS (lower than pure copper due to P content).
Corrosion Resistance: Excellent in water, refrigerants, and mild chemicals.
✔ Wetting & Flow Characteristics
Excellent wetting on copper/brass/bronze (forms smooth fillets).
Controlled viscosity (paste form) for precise application.
Capillary action: Works best with 0.05–0.2 mm joint gaps.
✔ Thermal & Chemical Stability
Service Temperature: Up to 200–250°C (avoid high-stress, high-temp environments).
Not for ferrous metals (steel, cast iron): Forms brittle Fe₃P phosphides.
Powder Metallurgy Sintering Braze Powder Joining Metal Components Customized
-
Composition & Alloy Types
Copper-Based (Cu, Cu-P, Cu-Sn, Cu-Ni):
CuP6/CuP8 (Self-fluxing): For copper/brass PM parts.
Cu-Sn (Bronze): Improves strength & wear resistance.
Iron & Steel-Based (Fe-Cu, Fe-Ni, Fe-Mn):
Fe-Cu (Common for structural parts): Enhances densification.
Fe-Ni (High-strength applications): Improves toughness.
Nickel-Based (Ni-Cr-B-Si, Ni-P):
High-temperature brazing (e.g., turbine components).
✔ Melting & Sintering Behavior
Liquid-Phase Sintering (LPS):
Forms a transient liquid phase at 800–1200°C, filling pores & improving density.
Solid-State Diffusion Bonding:
Some alloys (Fe-Cu) rely on solid-state diffusion for bonding.
✔ Mechanical & Physical Properties
Density Improvement: Reduces porosity by 5–15% vs. conventional sintering.
Tensile Strength: Can increase by 20–50% depending on alloy & sintering conditions.
Hardness & Wear Resistance: Enhanced by Ni or carbide additions.
✔ Wetting & Flow Characteristics
Controlled flow to prevent excessive spreading or distortion.
Optimized particle size (5–50 µm) for uniform distribution in the powder mix.
300 mesh brazing powder CuP8 copper welding powder bronze alloy powder has stable quality
-
✔ Composition & Melting Behavior
Alloy: Cu-7.5%P-0.2%Ag (common variant of CuP8).
Melting Range: 710–800°C (solidus-liquidus).
Self-Fluxing: Phosphorus (P) acts as a flux, removing oxides during heating (no separate flux needed for copper joints).
✔ Mechanical & Joint Strength
Shear Strength: ~150–220 MPa (depends on base metal and joint design).
Ductility: Moderate (better than high-P alloys like CuP10).
Electrical Conductivity: ~15–20% IACS (lower than pure Cu due to P content).
✔ Wetting & Flow Characteristics
Excellent wetting on copper & copper alloys (brass, bronze).
Not suitable for ferrous metals (steel, cast iron) – Forms brittle iron phosphides (Fe3P).
Best for capillary gap brazing (0.05–0.2 mm clearance).
✔ Corrosion & Thermal Resistance
Good corrosion resistance in water/refrigerant systems (used in HVAC, plumbing).
Service Temperature: Up to 200–250°C (avoid high-stress high-temp applications).
Fe-Si-Al Sendust Reduced Iron Metal Powder Magnetic Shielding EMI Suppression
-
✔ Magnetic Properties
High Permeability (μ): 50–120 (depends on composition & compaction).
Low Coercivity (Hc): <10 A/m → Reduced energy loss in alternating fields.
Saturation Magnetization (Bs): ~1.0–1.2 T (suitable for medium-power applications).
✔ Electrical & Thermal Performance
Low Core Loss (Pcv): Excellent for high-frequency (kHz–MHz) applications.
Good Thermal Stability: Maintains properties up to ~500°C.
High Resistivity (~80–150 μΩ·cm): Reduces eddy current losses.
✔ Mechanical & Chemical Properties
Soft & Ductile – Easily pressed into complex shapes.
Corrosion-Resistant – Forms a passive oxide layer (better than pure iron powder).
Lightweight (Density ~6.6 g/cm³) – Lighter than ferrites.
✔ Powder Characteristics (for Compaction & Sintering)
Particle Size: Typically 5–100 μm (adjustable for different applications).
Morphology: Irregular or spherical (depending on atomization method).
Binders Used: Epoxy, silicone, or phenolic resins for improved mechanical strength.
-
P5mm thick walls with thermal shock-resistant composition Mill Ceramic Jar
-
P99.95% purity Ultra High Purity 3Y-TZP Jar for Nanotechnology
-
PExtreme Environment Advanced Ceramic Grinding Jar 1500°C Capable
-
PEco-Friendly 95% Material Recovery Rate Recyclable Zirconia Ceramic Grinding Jar
-
PSolder Copper Phosphorus Metal Braze Paste 10g 500-800°C OEM
-
PPowder Metallurgy Sintering Braze Powder Joining Metal Components Customized
-
P300 mesh brazing powder CuP8 copper welding powder bronze alloy powder has stable quality
-
PFe-Si-Al Sendust Reduced Iron Metal Powder Magnetic Shielding EMI Suppression
-
POEM Fe-Cr-Ni Ferrous Iron Metal Powder Corrosion Resistant For 3D Printing
-
PCustom 3D Printing MIM Iron Metal Powder For Binder Jetting & SLM
-
P0.1mm 0.3mm Zirconia Milling Beads Grinding Balls Media White
-
PLab Grade Zirconia Grinding Media Ball Beads Contamination free For Battery Material Research
Leave a MessageWe will call you back quickly!